Strip Out construction: A Comprehensive Guide
Strip out construction, also known as demolition or deconstruction, is the process of removing interior or exterior elements of a building while preserving the structural integrity. It’s a crucial first step in many renovation, refurbishment, and redevelopment projects. Whether you’re planning a small-scale interior remodel or a large-scale commercial demolition, understanding the intricacies of strip out construction is essential for a successful project. This comprehensive guide will cover everything you need to know, from planning and preparation to execution and waste management.
Understanding the Scope of Strip Out
Strip out construction can range from removing a single wall to gutting an entire building. The scope of work can include:
Interior Strip Out: Removing non-structural walls, ceilings, Flooring, fixtures, mechanical and electrical systems, and other interior finishes.
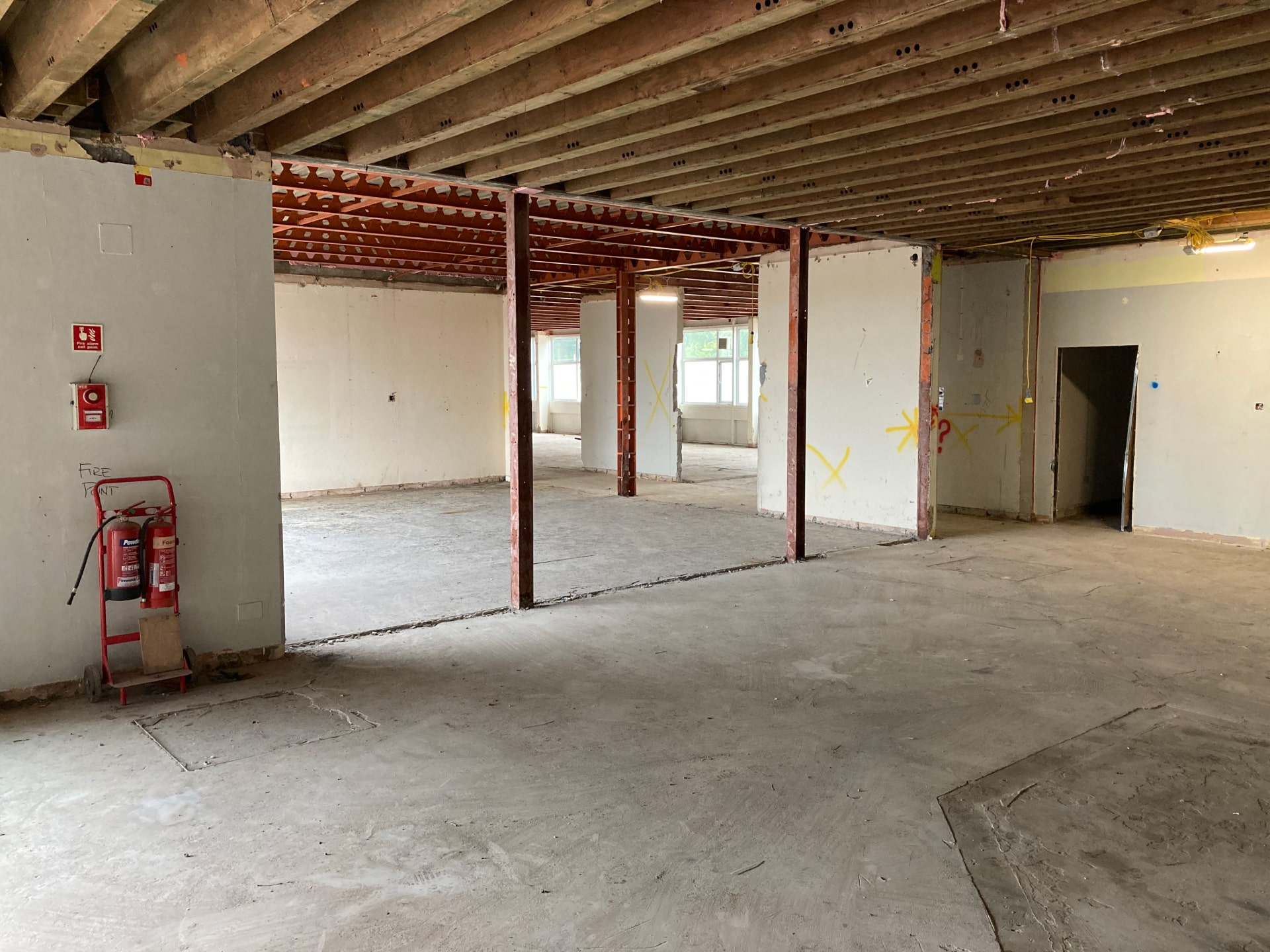
Planning and Preparation: The Foundation of Success
Proper planning is paramount for a smooth and efficient strip out project. Failing to plan can lead to delays, cost overruns, and even safety hazards. Here are the key steps involved in the planning process:
# 1. Project Assessment and Scope Definition
Detailed Survey: Conduct a thorough survey of the building to identify the materials used, the location of services (electrical, plumbing, gas), and any Potential hazards like asbestos or lead paint.
# 2. Health and Safety Considerations

Risk Assessment: Conduct a comprehensive risk assessment to identify potential hazards and implement appropriate control measures.
# 3. Waste Management and Disposal
Waste Audit: Conduct a waste audit to identify the types and quantities of waste materials that will be generated.
# 4. Contractor Selection
Qualified Contractors: Select experienced and licensed contractors who specialize in strip out construction. Check their credentials, insurance, and safety record.
Execution: Bringing the Plan to Life
Once the planning phase is complete, the execution phase can begin. This involves the actual physical removal of building elements.
# 1. Site Preparation
Site Security: Secure the site to prevent unauthorized access and ensure public safety.
# 2. Strip Out Process
Controlled Demolition: Use appropriate demolition techniques to minimize noise, dust, and vibration.
# 3. Debris Removal
Efficient Removal: Remove debris promptly and efficiently to maintain a safe and organized work site.
Waste Management: A Responsible Approach
Effective waste management is a crucial aspect of strip out construction. It not only helps to minimize environmental impact but also can contribute to cost savings.
# 1. Recycling and Reuse
Material Recovery: Identify materials that can be recycled or reused, such as wood, metal, and concrete.
# 2. Waste Disposal
Licensed Disposal Facilities: Ensure that all waste materials are disposed of at licensed waste disposal facilities in compliance with local regulations.
Post-Strip Out Activities
Once the strip out is complete, there are several post-strip out activities that need to be carried out.
# 1. Site Clearance
Debris Removal: Ensure that all debris and waste materials are removed from the site.
# 2. Inspections and Approvals
Inspections: Arrange for inspections by local authorities to ensure that the strip out work has been carried out in compliance with regulations.
Safety Considerations: A Top Priority
Safety is paramount throughout the entire strip out construction process.
# 1. Personal Protective Equipment (PPE)
Essential PPE: Ensure that all workers wear appropriate PPE, including hard hats, safety Glasses, gloves, and safety boots.
# 2. Safe Work Practices
Fall Protection: Implement fall protection measures when working at heights.
Conclusion
Strip out construction is a complex process that requires careful planning, execution, and waste management. By understanding the key steps involved and prioritizing safety, you can ensure a successful project that is completed on time and within budget. Remember to engage qualified professionals, prioritize recycling and responsible waste disposal, and always prioritize the safety of workers and the public. This comprehensive guide provides a solid foundation for understanding the intricacies of strip out construction. However, it is essential to consult with experienced professionals and local authorities for specific guidance related to your project.
strip out construction